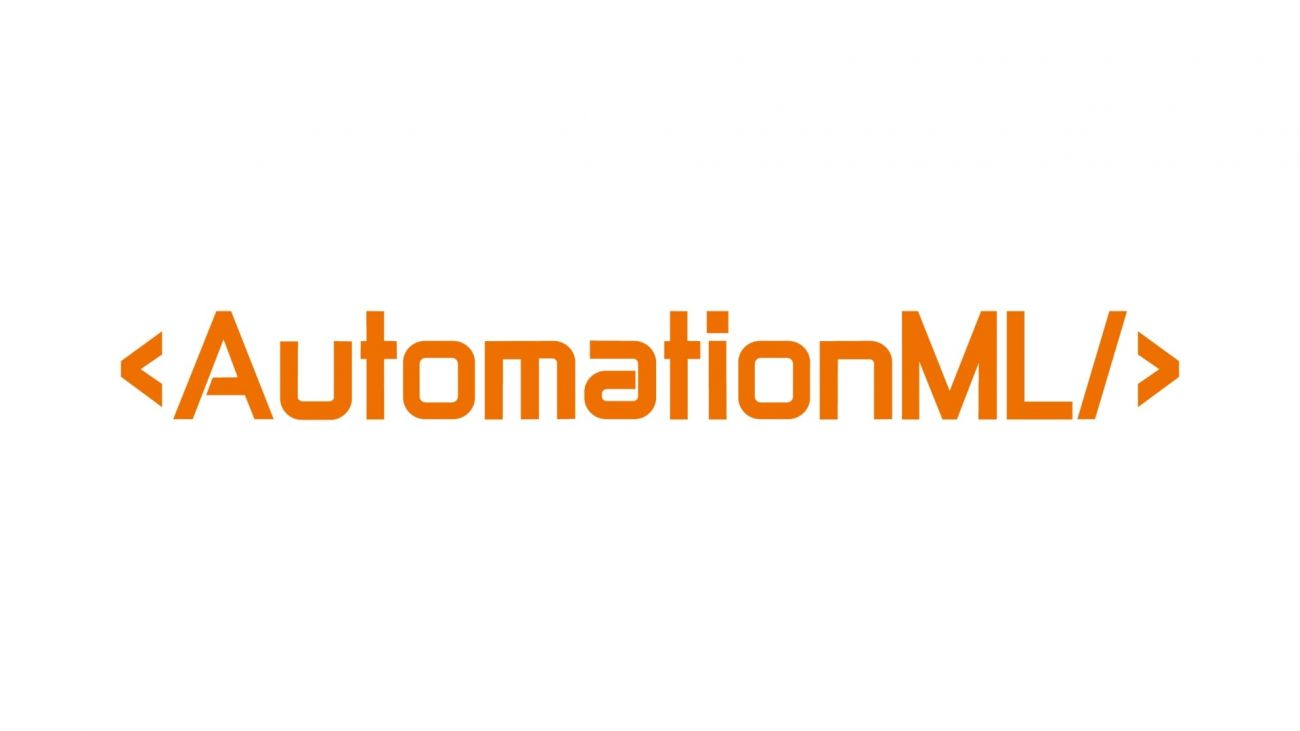
This application recommendation proposes a modelling method for mechanical aspects of drive configurations by means of the engineering data format AutomationML. Such information is e.g. required for drive capacity selection. It will describe the recommended use of role and interface classes as well as the recommended structures to be considered within the instance hierarchy of an AutomationML project.
The capacity selection of drives to be used in a factory or process automation application is very frequently recurring task. In this use case the information from the mechanical design of the machine needs to be transferred to the capacity selection software. This is often done by exchanging a paper form where the mechanical engineer enters the parameters and desired motion pattern and the application engineer calculates the required capacity of the drive.
In cases the mechanical design, its parameters or desired motion pattern is changed, the process needs to be started again. Additionally, the selected drive for one axis, might have an effect on another axis. So that roundtrip engineering becomes a desirable goal.
In the mechanical design a wide range of constructions is possible. But for the capacity selection they must be mapped to some standard “Load Mechanism” which can be used for the calculations. The goal is that a parameter change in the mechanical design is automatically reflected to the corresponding parameter in the load mechanism.
Additionally, many mid-range mechanical CAD tools support also simulation or motion analysis functionality. By using such simulation, the sizing of unknown/generic load mechanisms becomes possible. In such case the capacity selection tool receives only the simulation result and calculates the capacity based on those results.
Furthermore, the data exchanged between mechanical CAD tools and drive capacity selection tools can be seen as the base for the further engineering of the motion application and its software development. Additionally, the result of the capacity selection, namely the selected components such as inverter, motor, etc. are relevant for the E-CAD design of the machine or application or for product selection tools to select optionally required parts such as cables or connectors.
This application recommendation describes the workflows and the method of modelling mechanical aspects of drive configurations using AutomationML. It looks at the use case of capacity selection however it is not limited to only this use case.